热压罐设备与传统成型工艺在多个方面存在显著的差异。以下是对这两种成型工艺的对比分析:
一、设备结构与原理
热压罐设备
结构:热压罐是一个具有整体加热系统的大型压力容器,一端封闭,另一端开口,内部配有循环风扇以实现热量的均匀分布。
原理:将复合材料毛坯或预浸料用真空袋密封在模具上,然后放入热压罐中。通过加热和加压系统,对制品进行升温、加压、保温(中温或高温)、降温和泄压等处理,使其成为所需形状和质量的构件。
传统成型工艺
设备:传统成型工艺通常使用烤箱等设备来提供固化过程中所需的高温。
原理:将材料放入烤箱中,通过加热使其固化成型。但烤箱通常不能提供固化过程中所需的压力,因此可能需要配套多台设备才能完成整个固化过程。
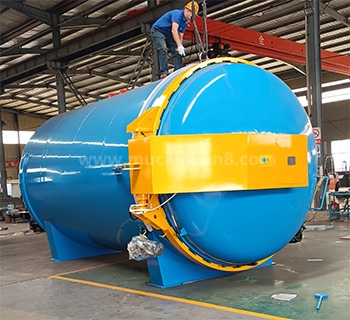
二、成型效果与适用范围
热压罐设备
成型效果:
制件尺寸稳定,重复性好。通过精确控制温度、压力和时间等参数,可以确保制品的尺寸精度和形状稳定性。
力学性能可靠。可制造纤维体积含量高(60%~65%)的复合材料制品,这些制品具有较高的强度和刚度。
孔隙率低,树脂含量可控。通过均匀的压力和温度分布,可以实现制品内部的高质量固化。
适用范围:适用于各种工装和形状复杂的复合材料制品,特别是对于大型制品和复杂曲面的加工具有独特优势。广泛应用于航空航天、汽车制造、船艇工业以及高端消费品等领域。
传统成型工艺
成型效果:受限于烤箱的加热方式和温度控制精度,传统成型工艺可能无法实现均匀的温度分布和压力控制,从而影响制品的成型质量和力学性能。
适用范围:通常适用于形状简单、尺寸较小的复合材料制品的固化成型。在某些特定领域,如汽车配件改装等,传统成型工艺仍有一定的应用空间。
三、生产效率与成本
热压罐设备
生产效率:单次可以生产多个制品,且固化周期相对较短(尽管对于某些高温高压材料可能较长),因此具有较高的生产效率。
成本:热压罐设备体积大、结构复杂,且是压力容器,因此建设投资费用较高。同时,每次固化时都需要制备真空密封系统,这将耗费大量价格昂贵的辅助材料(如真空袋、密封胶条等),提高了制造成本。
传统成型工艺
生产效率:单次只能生产一个制品,且固化周期可能较长(因为需要等待烤箱升温至所需温度并保持一段时间),因此生产效率相对较低。
成本:虽然传统成型工艺的设备成本相对较低,但由于生产效率低且需要配套多台设备才能完成整个固化过程,因此整体成本可能并不低。
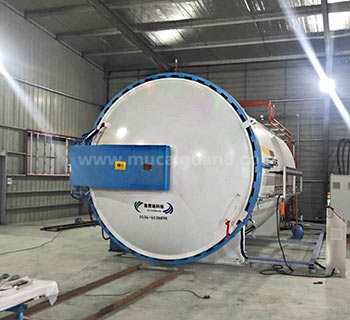
四、环保与能耗
热压罐设备
环保:热压罐成型工艺通常使用惰性气体(如氮气)作为加压介质,避免了空气自燃的危险。同时,通过精确控制温度和压力等参数,可以减少能源消耗和废弃物排放。
能耗:虽然热压罐设备在运行时需要消耗大量的电能和热能,但由于其高效的加热和加压系统以及保温系统,可以降低能源浪费并提高能源使用效率。
传统成型工艺
环保:传统成型工艺在固化过程中可能产生有害物质排放(如挥发性有机化合物等),对环境造成一定影响。同时,由于烤箱的加热方式不够均匀且可能产生热损失,因此其环保性能相对较差。
能耗:传统成型工艺在固化过程中需要消耗大量的电能和热能,且由于加热方式不够高效和均匀,因此能源浪费现象较为严重。